10 Essential Checks for Successful Pre-Production Inspections
- PARTH PATEL
- Jan 10
- 3 min read
Pre-production inspections are crucial for ensuring a smooth manufacturing process. By verifying raw materials, components, and production setups before manufacturing starts, businesses can avoid costly defects and delays. In fact, studies show that effective pre-production inspections can reduce product returns by up to 30%, significantly saving time and money.
In this post, we will explore ten essential checks that must be conducted during pre-production inspections. By addressing these items, you can set the stage for a successful production run.
1. Material Quality Verification (Pre-Production Inspections)
Assessing the quality of raw materials is the first step in any successful production process. Inspect samples for physical properties to confirm they meet the required specifications. For instance, if you're working with metals, check for tensile strength and corrosion resistance. According to industry standards, 80% of production issues can be traced back to inferior quality materials.
Additionally, ensure that materials have the necessary certifications. For example, materials used in food production should comply with FDA regulations. This level of scrutiny helps prevent problems later on.
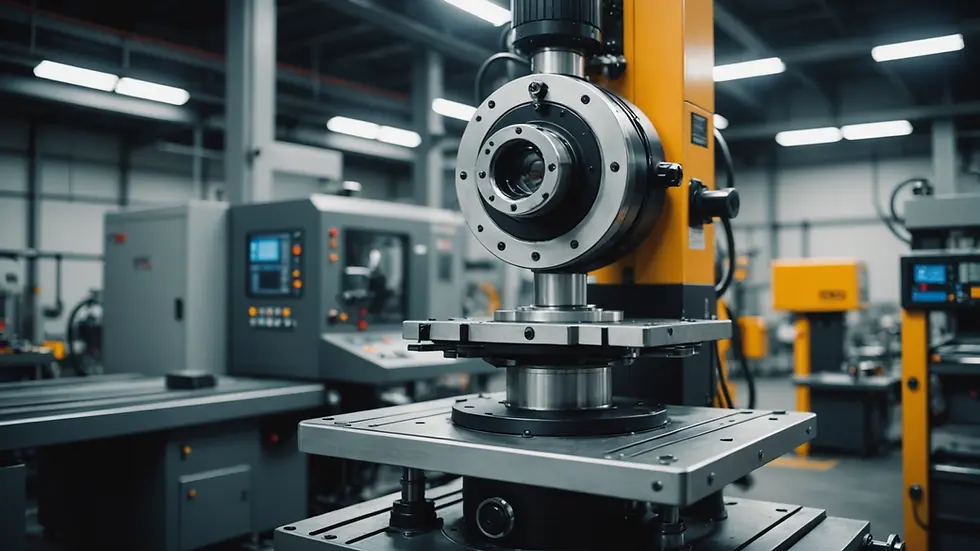
2. Component Compatibility
It is vital to verify that all components are compatible with one another. This involves a close examination of specifications. Additionally, confirming that parts fit together correctly can save your team significant time. Data shows that assembly errors can cost manufacturers up to $50,000 a day in downtime.
Request documentation from suppliers to confirm compatibility. This small step can activate adjustments before production, ensuring a smoother assembly process.
3. Equipment Calibration
Before starting production, ensure that all machinery and equipment are properly calibrated. Uncalibrated machines can lead to inconsistencies, affecting up to 25% of production quality. Regular calibration checks can mitigate these risks by ensuring that machines operate at optimal performance.
Maintain a log of calibration dates and results to track compliance over time. This habit contributes to accountability and precision in your production processes.
4. Production Setup Review
Conduct a thorough review of your production setup. Analyze workflows to see if the layout maximizes efficiency. For example, using Lean Manufacturing principles, you can arrange workstations based on the order of operations, reducing travel time for team members.
Identify areas that require adjustments, like tool placement or material flow. A well-organized production line can increase your operational efficiency by up to 20%.
5. Safety Standards Compliance
Safety standards should always be a priority. Inspect the production area to ensure compliance with safety regulations. Chances are, addressing just one potential hazard can save thousands in potential injury claims. Moreover, training staff on safety protocols can enhance workplace safety and efficiency.
Consider conducting a safety drill before production begins. Engaging your team in safety practice can reinforce your commitment to their well-being.
6. Supplier Documentation
Thoroughly review all supplier documentation. Ensure contracts, invoices, and delivery schedules are in sync with the production timeline. Misalignment can lead to unexpected delays.
Effective communication with suppliers is key. Building solid relationships can enhance reliability, ensuring you receive materials on time and according to specifications.
7. Prototype Inspection
If applicable, inspect prototypes to verify design specifications and functionality. This step can reveal design flaws before mass production starts, potentially avoiding costly errors. Feedback gathered during this stage can lead to significant improvements.
For example, Apple uses prototype testing extensively to gather data on usability. Early insights can lead to enhancements that improve the final product's success.
8. Visual Inspection of Final Assembly
Before the official start of production, conduct a final visual inspection of the assembly setup. Verify that every part is in position and functioning correctly. Check tools, processes, and resources to be sure you are fully prepared for production.
This quick yet essential step can identify any last-minute adjustments that need addressing.
9. Inventory Check
Finally, verify that your inventory levels are sufficient for production. This includes checking for an adequate supply of materials, components, and tools. Disruptions due to shortages can lead to downtime, costing you both time and money.
Implement a clear inventory management system to track materials effectively. Keeping your inventory organized can help ensure that everything is ready when you need it.
10. Feedback Mechanism
Establishing a feedback mechanism encourages continuous improvement. Create simple channels for team members to share their experiences during the pre-production inspection process. Engaging your team can highlight overlooked elements or recurring issues.
Documenting feedback acts as a valuable resource for future projects. This proactive approach helps build a culture of continuous improvement within your organization.
Final Thoughts
Pre-production inspections are crucial for successful manufacturing. By conducting the ten essential checks outlined in this post, businesses can minimize defects and delays. This not only leads to higher product quality but also boosts overall efficiency.
Incorporating these checks into your manufacturing process enhances reliability. This builds trust with clients and stakeholders. Remember, thorough preparation is the key to seamless production—let these essential checks guide your pre-production inspections.
Comments